Click here to view my auctions on EBAY
 |
 |
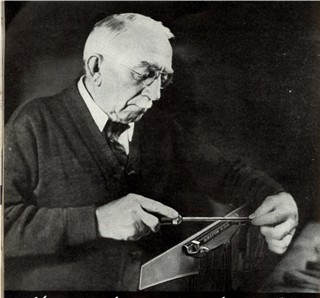 Henry Disston, in his early years of saw making, was obliged to use foreign made steel. Having difficulty in obtaining high grade steel of uniform quality which he required for the production of hand saws, he determined to make his own steel. He then set about mastering the art of steel making, turning to crucible steel in order to obtain the highest grade steel of that day.
In 1855 Henry Disston built his own furnaces and melted the first Crucible Saw Steel ever made in America, becoming a pioneer in fine steel making. From that day on, Disston has been making its own saw and tool steel.
In 1906, faced with the necessity of making steel on larger heats, Disston again made a pioneering step. Electricity was used in heating the furnace and the first commercial heat of Elecric Tool Steel of crucible quality ever made in America was cast in the Disston plant. Since then, Heroult electric Furnaces, capable of pouring from three to six tons at a heat, have been placed in operation.
The steel mill in the Disston plant today is equipped with modern steam hammers, steel rolling mills, annealing furnaces and all other modern devices for making high grade saw and tool steels. HEat is controlled in the furnaces to the closest degree by pyrometers; testing is done by skilled men in the laboratories under the close supervision of Disston's nationally known metallurgists. Exacting tests and laboratory checks control the output of the Disston Steel Works at all times.
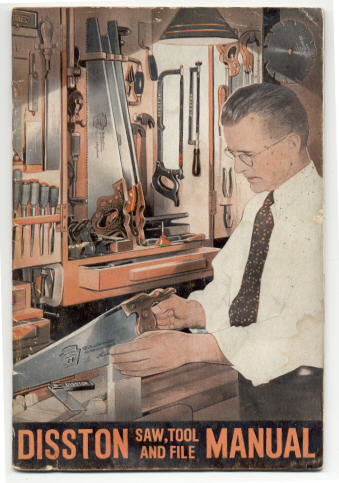 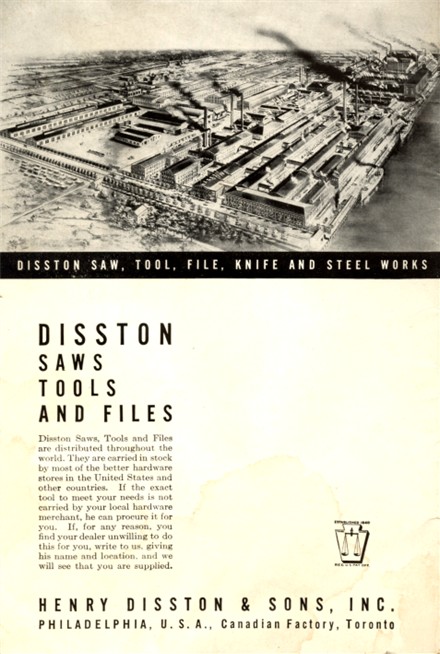
|
This information is from a 1941 Disston Saw, Tool and File Manual.
Disston Saws, Tools and Files are distributed throughout the world. They are carried in stock by most of the better hardware stores in the United States and other countries. If the exact tool to meet your needs is not carried by your local hardware merchant, he can procure it for you. If, for any reason, you find your dealer unwilling to this for you, write to us, giving his name and location, and we will see that you are supplied.
For one hundred uears, Henry Disston & Sons, Inc., Philadelphia, has been manufacturing the saw that- "For Beauty, Finish and Utility--cannot be excelled". Disston Saws, tools and Files have done much to improve both wood and metal working the world over. When a need arose for a new type of saw, a better saw or a more efficient saw, Disston created it.
101 Years of Disston Leadership. In the United States, before 1840, American carpenters used saws made in Europe. Henry Disston, however, felt that he could make a finer saw than the European manufacturers, so he set to work in a cellar in Philadelphia.
Henry Disston was then twenty-one years old, a young man with vision, for he saw a need that he could fulfil. It was necessary to create a finer saw than the imported tool then in use, for the existant demand was for foreign saws.
Within a few years, saws made by Disston and his skilled workmen became know as "The Saw Most Carpenters Use". Demand for foreign saws gave way to American workmanship and the Disston Saw Works was well under way. In time, foreign demand for quality tools and saws created export trade for Disston. Today, there is not a place in the world where tools are used, which does not know the name Disston.
For a century, Disston has made advance after advance in the production of high grade saws. Today, Disston is looked upon as the leader in saw manufacturing.
Click here for more interesting history on Disston |
|  |
 |
 |
 |
Airmaster |
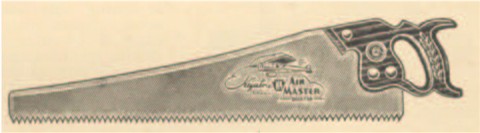
|
Air Master Skew Back
Neatly finished. Thin back. Teeth bevel filed. carved handle stained gun metal. Lenght cutting edge 26 inches. Four screws.
Points per inch 8.
Challenger Skew Back
Taper ground. Extra high finish. Teeth bevel filed. Full carved hardwood handle stained light brown. Length cutting edge 26 inches. Five screws.
Points per inch 8
Defender |
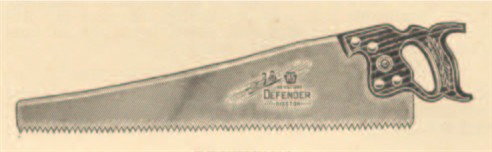
|
Defender Skew Back
Extra high finish. Thin back. Teeth bevel filed. Carved handle stained light brown. Length cutting edge 26 inches. Five screws.
Points per inch 8.
Pacemaker |
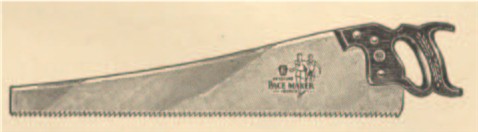
|
Pacemaker Skew Back
Crosscut
Carved hardwood handle, mahogany color. Length cutting edge 20 inches. Four screws. Points per inch 9.
Pacemaker Skew Back
Crosscut
Length cutting edge 26 inches. Four screws.
Points per inch 8.
Leader |
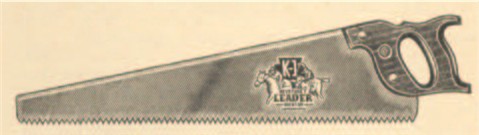
|
Leader Straight Back
Cross Cut
Hardwood handle stained. Length cutting edge 26 inches. Three screws.
Points per inch 8.
Speedster |
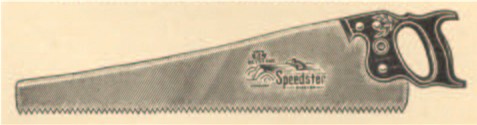
|
Speedster Skew Back
Cross Cut
Carved hardwood handle stained cherry color. Length cutting edge 26 inches.
Four screws. Points per inch 8.
D7S |

|
D7S Ship Pattern
Straight Back Hand
Crucible steel blade, polished, striped back, true-taper ground. Beechwood handle, weatherproof finsih, with covered top and brass screws. Length cutting edge 26 inches, width blade at butt 6 1/4 inches, at point 1 1/2 inches.
Four screws. Points per inch 7,8 and 9.
D8S |
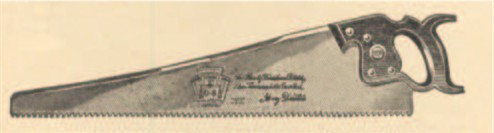
|
D8S Light Weight or Ship Pattern
Skew Back Hand
Refined crucible steel blade, polished, striped back, true taper ground. Applewood handle, weatherproof finsish, with covered top and brass screws. Length cutting edge 26 inches. Width blade, at butt 5 7/8 inches, at point 1 1/2 inches. Four screws. Points per inch 7,8 and 9.
D-8 |
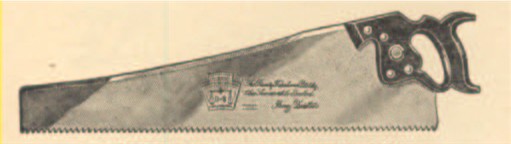
|
D8 Regular Pattern
Skew Back Hand
Refined crucible steel blade, polished, striped back, true taper ground. Applewood handle, weatherproof finish, with covered top and brass screws. Length cutting edge 26 inches. Width blade, at butt 6 5/8 inches, at point 2 11/16 inches. Five screws. Points per inch 7,8,9,10 and 11.
D8R Rip
Same as above but points per inch 5,5 1/2 and 6.
Panel D8/20
Length cutting edge 20 inches, width blade at butt 5 1/8 inches, width blade at point 2 1/8 inches, points per inch 9 and 10.
Panel D8/22
Length cutting edge 22 inches, width blade at butt 5 1/2 inches, width blade at point 2 1/4 inches, points per inch 9 and 10.
D-23 |
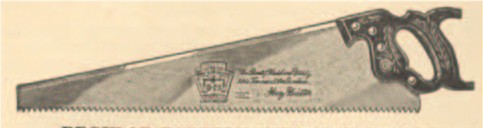
|
D23/26 Regular Pattern
Straight Back Hand
Refined crucible steel blade, highly polished, striped back, true taper ground. Full carved applewood handle, weatherproof finsih, with covered top and brass screws. Length cutting edge 26 inches. Width blade at butt 5 7/8 inches, at point 1 1/2 inches five screws. Points per inch 7,8,9,10,11 and 12.
D23/26 Rip
Same as above but points per inch 5 1/2 and 6.
|
|
|
|  |
 |
|